Introduction to Crossed Roller Bearings
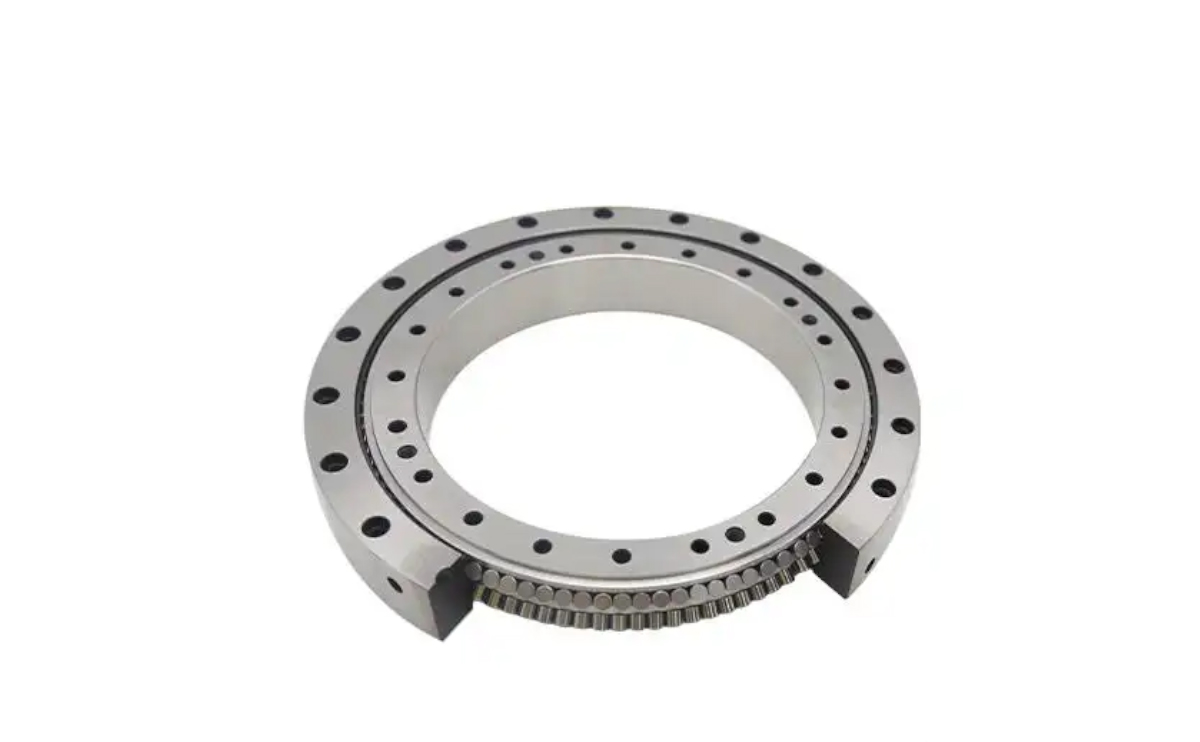
Crossed roller bearings are a special type of bearing with a split inner ring and a rotating outer ring. Due to their special structure, they are commonly used as joint bearings in industrial robots.
Crossed tapered roller bearings are designed to provide high rotational accuracy and stiffness in a small space, with substantial material cost savings. These bearings are made by mounting two sets of bearing races and rollers in a right-angled criss-cross, with adjacent rollers facing in opposite directions, with isolation blocks mounted between the rollers, and with support shims on the rollers, which allows the two half-rows of rollers to fit into the same space.
The bearing’s angular and tapered geometry makes its effective span several times larger than its actual width.
Crossed roller bearings are high-precision bearings with a special structure, which are widely used in industrial robots, precision machine tools, medical equipment, and other fields. Unlike conventional bearings, the structure of crossed roller bearings is carefully designed so that they can withstand large loads in a limited space.
How is the structure of crossed roller bearings?
inner and outer ring, are equipped with V-shaped groove raceway, roller ends and groove contact line into a straight line, as a support to guide the roller movement of the track, the inner ring is mounted on the shaft, the outer ring is mounted on the housing or bracket, in order to ensure the durability and rigidity of the crossed roller bearings, generally made of high-strength materials.
Rollers, the use of cylindrical rollers and 90-degree cross arrangement, can simultaneously withstand radial, axial, and tilting moments, bearing capacity is relatively strong.
A cage or isolation block, is used to separate the rollers, prevent the rollers from contacting each other, reduce friction, wear and tear, improve bearing life, and maintain stable operation.
Related Products
Crossed roller bearings use characteristics introduction
High load-carrying capacity. Crossed roller bearings inside the roller to 90 degrees cross arrangement, and along the raceway contact, this structure can simultaneously withstand radial, axial, and tilting moments, its load carrying capacity far more than ordinary ball bearings. If the material is good, the bearing capacity is even higher.
Good rigidity and high precision. Crossed roller bearings should be preloaded design, so as to eliminate axial and radial clearance, improve rigidity, reduce deformation error, and are suitable for high-precision equipment, such as industrial robot joints, precision machine tools rotary tables.
Space saving. Bearing internal roller cross-arrangement, high space utilization, can provide greater support rigidity in a smaller size, more suitable for use in space constraints but with high precision requirements of the application.
Smooth running. As the roller adopts the line contact form, rolling resistance is small, the bearing runs more smoothly, reduces energy loss, and improves the operating efficiency of the equipment.
Easy installation. Crossed roller bearings can withstand multiple directions of force at the same time, do not need too complex a support structure, and can reduce processing, and installation costs.